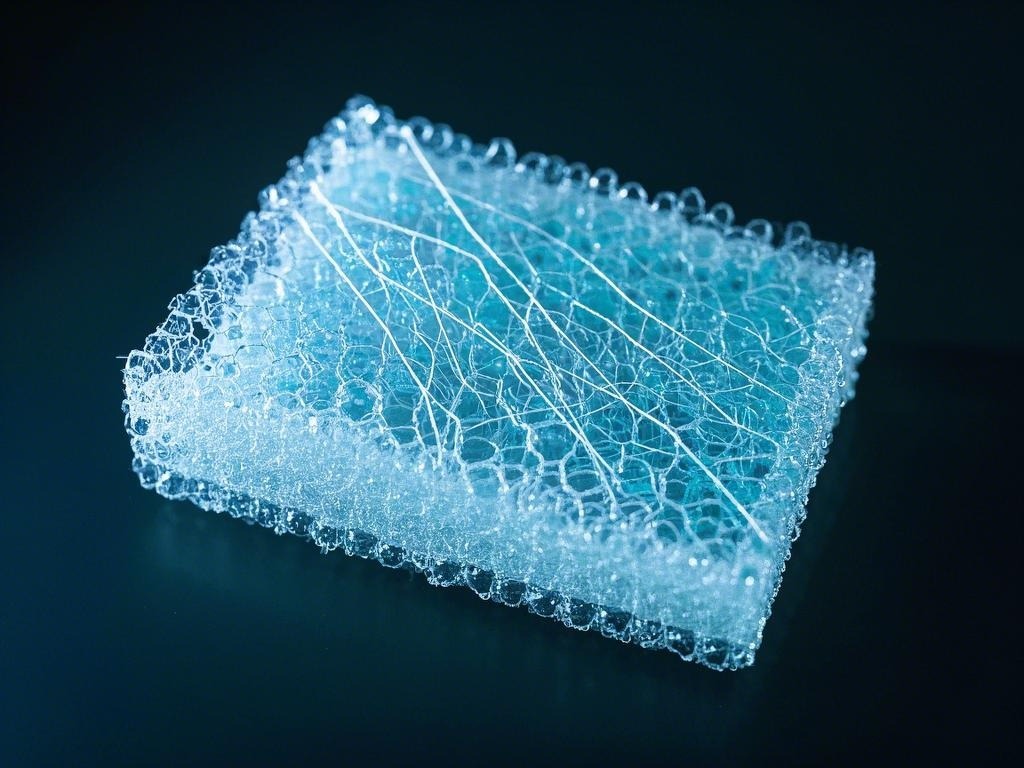
1. Introduction
The glass fiber aerogel blanket (GFAB) represents a revolutionary advancement in thermal management materials, combining the mechanical robustness of glass fiber reinforcement 15 with the ultra-low thermal conductivity of silica aerogels (0.015-0.025 W/m·K). First commercialized in the early 2010s, GFABs now serve critical roles across energy-intensive industries where traditional insulation fails to meet modern efficiency demands.
2. Structural Compositiong & Manufacturing
2.1 Core Components
- Glass Fiber Matrix: Typically uses 5-9μm diameter fibers with SiO₂ content >95% 7, providing:
- Tensile strength up to 1.5 MPa
- Operational temperature range: -200°C to 650°C
- Chemical resistance to acids/alkalis (pH 1-12)
- Aerogel Infusion: Silica aerogel particles (2-5nm pores) occupy 85%-92% void space 3
2.2 Advanced Fabrication Techniques
- Modified Sol-Gel Process: Incorporates surface-treated glass fibers 1 to enhance aerogel adhesion
- Ambient Pressure Drying: Reduces energy costs by 40% vs traditional supercritical methods 9
- Hybrid Reinforcement: Some formulations integrate fly ash particles 1 for improved compressive strength
3. Performance Advantages
3.1 Thermal Characteristics
Property | GFAB | Mineral Wool | Ceramic Fiber |
---|---|---|---|
Conductivity (W/m·K) | 0.018 | 0.040 | 0.12 |
Thickness Efficiency | 1X | 2.2X | 6.7X |
Service Life (years) | 20+ | 7-10 | 3-5 |
3.2 Mechanical & Safety Features
- Fire Resistance: Meets ASTM E84 Class A (flame spread <25)
- Vibration Endurance: Maintains integrity under 15G vibration 5
- Hydrophobicity: <2% water absorption after 24h immersion
4. Industrial Applications
4.1 Oil & Gas Infrastructure
- Pipeline insulation reduces heat loss by 60% vs conventional materials 2
- Case Study: Aramco’s Ghawar Field achieved 18% fuel savings in crude transmission
4.2 Power Generation
- Turbine exhaust insulation improves combined cycle efficiency by 1.2-1.8%
- Nuclear applications: Withstands LOCA conditions (170°C steam for 72h)
4.3 Transportation
- Lightweighting (3.5kg/m³ vs 100kg/m³ for rock wool) enables:
- 8-12% fuel savings in maritime shipping
- 15% weight reduction in aerospace thermal protection systems 7
5. Technical Challenges & Innovations
5.1 Current Limitations
- Brittle edges requiring protective facings
- 30-45% cost premium over traditional materials
5.2 Emerging Solutions
- Fiber Hybridization: Blending glass fibers with PBO fibers increases flexibility by 200% 5
- AI-Optimized Manufacturing: Machine learning algorithms reduce drying time variability by 18% 9
- Recycling Systems: Closed-loop processes recover >85% silica content 2
6. Future Outlook
The GFAB market is projected to grow at 11.2% CAGR through 2030, driven by:
- Strictening ISO 50001 energy standards
- Hydrogen economy demands for cryogenic insulation
- Space exploration requiring ultra-light thermal barriers